リーンオペレーションとは?ポイントをわかりやすく解説
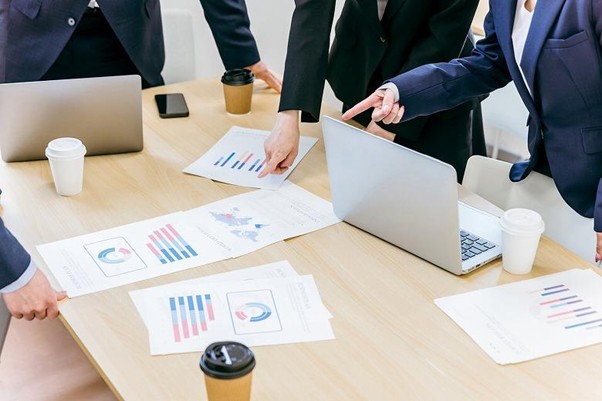
「この作業、もっと効率的にできないだろうか?」「人件費を抑えながら、生産性を上げる方法はないのか?」 リーンオペレーションを活用すれば、このような悩みを解決できるかもしれません。実際、多くの日本企業が業務効率化を経営課題として挙げています。
しかし、やみくもに効率化を進めると、かえって品質の低下や従業員の不満を招くリスクがあります。単なるコスト削減だけでは、企業の長期的な成長は望めません。
そこで注目を集めているのが「リーンオペレーション」という考え方です。これを実施することで、ムダを徹底的に排除しながら、品質と従業員満足度を向上させることができます。
本記事では、「リーンオペレーションの基本的な考え方」について解説し、さらに「リーンオペレーションに取り組む手順」についても紹介します。ぜひ参考にしてください。
リーンオペレーションとは
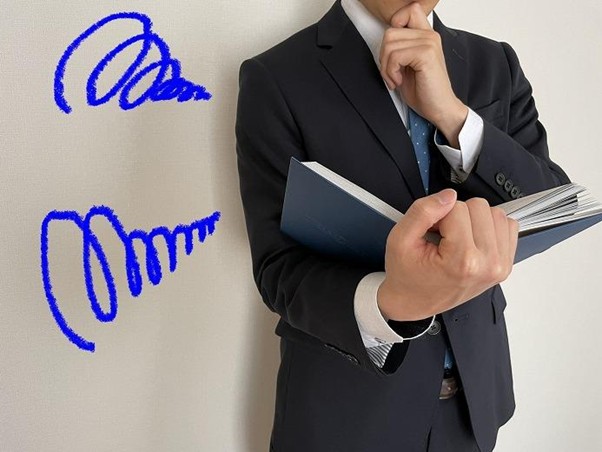
リーンオペレーションとは、英語の「lean(贅肉をそぎ落とす)」に由来する手法です。無駄を排除し、リソースを最適に活用することで、生産性や顧客価値の最大化を目指します。この「リーン」という考え方は、さまざまな業界で活用されています。例えば、トヨタ自動車が生み出した「トヨタ生産方式」をベースとする「リーン生産方式」も、その一例です。
リーンオペレーションの本質は、ムダな作業、過剰な在庫、不要な手順を見直し、本当に必要な工程だけを残すことにあります。一見すると製造業向けの手法に思えますが、実際にはサービス業や小売業など、さまざまな業種で活用できます。リーンオペレーションを導入し、企業の体質をスリム化することで、コスト削減と業務効率の向上を同時に実現できるでしょう。
リーンオペレーションの目的
リーンオペレーションの根本的な目的は、企業価値の最大化です。単にムダを省くだけでなく、顧客満足度を向上させながら、利益を生み出す仕組みを構築することを目指します。
その最たる例が、業務プロセスの見直しによる従業員一人ひとりの作業効率の向上です。結果として、残業時間の削減や職場環境の改善につながり、企業全体の生産性向上と従業員満足度の向上が期待できます。また、ムダを省くことで生まれた時間的・経済的余裕を再投資すれば、企業の競争力を強化できます。継続的な取り組みによって、持続的な成長が可能となるのです。
リーンオペレーションの5つの要素
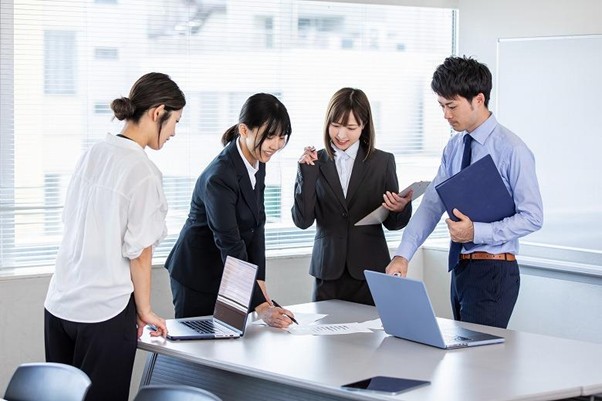
リーンオペレーションを成功させるには、5つの要素の最適化が不可欠です。各要素をバランス良く改善し、効率的な業務運営を実現していかなくてはいけません。
そのためにも、以下の5つの要素は必ず理解しておきましょう。
1.ヒト
人材は企業の最も重要な資産です。リーンオペレーションでは、従業員一人ひとりのスキルと経験を最大限に活用します。
- 業務遂行に必要なスキルは何か
- スキルを保有しているのは誰か
- 人材の数は適正か
これらを把握した上で、必要に応じて教育研修や権限委譲を行い、従業員の主体性を引き出します。業務の属人化を防ぎ、誰もが同じ品質で仕事ができる環境を整えましょう。
2.モノ
設備や在庫などの物的資源を効率的に活用することも、リーンオペレーションの重要なポイントです。
- 必要以上の在庫を持たない
- 設備の稼働率を最適化し、コストを抑制する
- 道具や設備は、業務に必要十分なものを選ぶ
最新・高性能な設備が必ずしも最適とは限りません。定期的な棚卸しと分析を行い、本当に必要なものを見極めましょう。
3.時間
リーンオペレーションでは、時間の有効活用も重要です。ムダな待ち時間や重複作業を排除し、業務の効率を高めます。
- 作業の所要時間を測定・分析し、ボトルネックを特定する
- 作業工程を可視化し、ムダな時間を発見する
- 改善策を講じ、全体の作業効率を向上させる
業務の流れを一度可視化すると、思わぬムダが見つかることもあります。継続的な見直しを行い、作業の最適化を図りましょう。
4.プロセス
業務の流れを可視化し、無駄な工程を徹底的に見直します。部門間の連携を強化し、情報共有をスムーズにすることで作業の重複を防ぎます。
- 既存の業務プロセスを定期的に見直す
- 標準化された業務プロセスを確立する
- 定量的に業務を把握し、具体的な流れを可視化する
プロセスを明確にすれば、品質のバラつきを抑制し、誰が実施しても同じ結果を得られる仕組みを作ることができます。
5.ルール
明確なルールと基準の設定は、効率的な業務運営の基盤となります。
- 行動の規範を定める
- 従業員が重視すべき価値観を示す
ルールがあることで、社内全体の価値観や行動が統一され、全員が同じ方向を向いて業務を遂行しやすくなります。ただし、曖昧なルールでは従業員が理解しにくいため、短いフレーズで直感的に理解できるよう工夫しましょう。
リーンオペレーションの5つのステップ
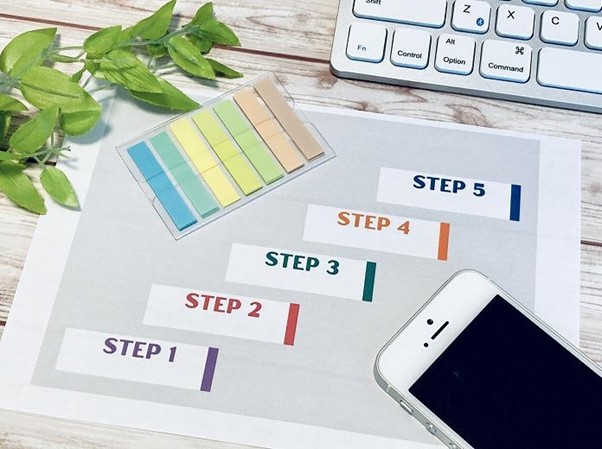
ここからはリーンオペレーションを実現するための手順を紹介します。以下の順番に進めましょう。
Step1.可視化で業務の全体像を洗い出す
リーンオペレーションを実現するにあたり、まずは業務プロセスの現状を見える化します。作業時間、コスト、人員配置などの情報を数値化し、課題を特定しましょう。以下の流れで可視化を進めます。
- 業務アセスメント(業務の全体像を洗い出す)
- 業務工数の推計
- 必要スキルとツールの整理
- 業務原則や従業員の意識の測定
最初に業務全体を把握し、そこから業務工数や必要なスキルを明確化することで、改善すべきポイントを特定できます。
特に、従業員の意識の測定には注意が必要です。数値だけでは把握しにくいため、アンケートを実施し、従業員の意見を収集しましょう。
Step2.標準化しプロセスを統一する
次に、業務の基準を定めてプロセスを統一し、標準化を進めます。誰もが同じ品質で業務を遂行できるよう、明確な基準を設定しましょう。効率的な業務プロセスを確立し、標準作業手順として文書化すると、さらに効果的です。
標準化の際に定めるべき要素は、以下の5つです。
- 道具
- 動作
- 手順
- スキル
- 時間
これらを基にマニュアルやチェックリストを作成することで、作業の漏れやミスを防ぎ、再現性を高めることができます。
Step3.単純化で業務のムダを排除する
標準化が完了したら、業務プロセスの簡素化を進めます。不要な承認手続きや重複する作業を廃止し、より効率的な業務フローを作成しましょう。その際、以下の「ECRSの法則」を活用すると効果的です。
- Eliminate(なくす):不要な業務や工程を完全に取り除く
- Combine(寄せる):分散している業務や工程を統合する
- Rearrange(順序を変える):業務の順序や配置を最適化する
- Simplify(簡素化する):業務を簡素化し、誰でも理解・実行しやすくする
業務を単に「続けるか・やめるか」ではなく、必要性に基づいて精査し、最適な形に整えましょう。
Step4.徹底化でスリム化した業務を定着させる
単純化したプロセスを組織全体に定着させるため、定期的な研修や実践的な訓練を行い、全従業員のスキル向上を図ります。改善されたプロセスを持続的に活用し、効果を最大限に発揮できるようにすることが目的です。
徹底化の流れは以下のとおりです。
- 通知:社内通達などで従業員に新プロセスの導入を知らせる
- 理解:マニュアルや勉強会を通じて、新プロセスを理解できるようにする
- 実践:実践的な研修を実施し、新プロセスを定着させる
- 確認:継続的にプロセスをチェックし、改善を続ける
リーンオペレーションは一度実施して終わるものではなく、PDCAサイクルを回しながら継続的に改善していくことが重要です。
Step5.価値強化された製品やサービスを提供する
最後に、リーンオペレーションによる業務の効率化を基に、提供する商品やサービスの価値を高めていきます。業務のムダを排除した後、余ったリソースを新たな価値創造に活用することで、競争力を強化できます。
ここまでのステップを実行することで、リーンオペレーションの実現が可能になります。業務の最適化によって生まれた余力を、顧客満足度の向上や新規事業の開発など、企業の成長につながる取り組みに活かしましょう。
まとめ
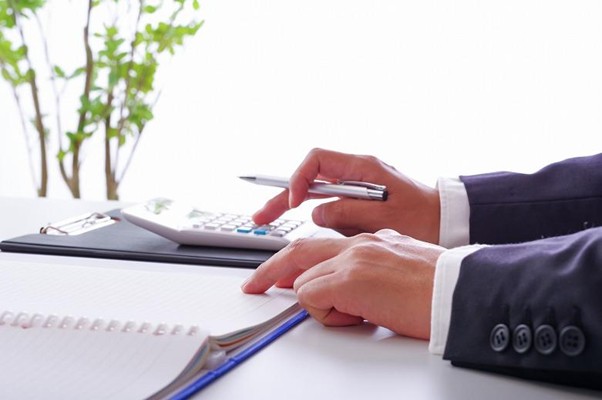
リーンオペレーションを実現するためには、業務の 可視化・標準化・単純化・徹底化・価値強化 の5つのステップを順番に進めることが重要です。
まず現状を明確にし、業務プロセスを統一・最適化することでムダを削減。その後、新しいプロセスを組織全体に浸透させ、継続的に改善を行います。
最終的には、効率化によって生まれたリソースを活用し、より高い価値を持つ製品やサービスの提供につなげることができます。